Shortcuts created long-term problems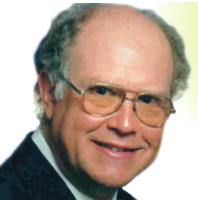
I did some work for Boeing Commercial Airplanes in the late ‘80s. Back then, the Japanese were taking market share in many industries by producing very high-quality products.
I worked for Digital Equipment, and we were running several study missions to Japan for senior executives to learn what the Japanese were doing, so we could become even more competitive, too.
We decided to begin with a joint quality seminar with a major customer also very concerned with the quality of their products: Boeing in Seattle. I got to teach it.
We had to read six books and 40 Harvard Business Review-type papers before we left Boston — education we needed to understand what we would see in Japan.
In Washington, we had the seminar and toured Boeing’s facility in Everett, where they were building 747s. Part of the deal was that I would have to return to Boeing and explain what we learned in Japan.
Even though the study mission schedule was grueling, it went incredibly well.
Several weeks after we got back, I went back to Seattle to do the presentation. They loved it and invited me back to do it at a two-day workshop for 400 senior managers.
They only had one criticism. As a former pilot, I used a picture of a Beechcraft instrument panel to explain what the instruments do for the pilot and what statistical tools do for the manager.
“Why are you using such a dinky instrument panel? Why not use one of ours?”
“Send me one and I’ll use it!” They sent me a picture of a 747 instrument panel. Now, I was ready and went back to Seattle.
At breakfast, we had an interesting discussion about quality with people who were actively pursuing it. I participated in their workshop all day and met their VPs plus a few more for dinner in a private dining room that evening. It was a grueling session.
Most of these guys were pilots. They didn’t fly Boeing airplanes; they flew small private planes, but they understood aviation. When an airplane gets into trouble, you can’t pull over to the side of the sky and call AAA to fix the problem or tow you to a garage.
Many Boeing airplanes have over a million parts, and they all have to work well together. When an airplane crashes because of a mechanical failure, 99% of the parts are still working just fine. It’s a daunting challenge to make sure those critical failures never happen. If they do, the onus is on finding out exactly what happened so they can prevent it from ever happening again.
These guys weren’t pretending. They often flew on Boeing airplanes for business. They flew with their families for vacations. I could tell they were very serious about ensuring the safety and reliability of every airplane they produced. Unfortunately, they’re retired now.
The Boeing we’re reading about today seems to have succumbed to the malaise that is destroying too many of our companies. If we can believe the news reports, their current CEO from GE and many senior managers may not understand that profitable shortcuts in aircraft design and production can be deadly and costly.
Boeing airplanes have been in the news an awful lot lately, but it’s not always a Boeing problem. When a tire falls off a plane on takeoff, and that plane has been in service for several years, that’s not Boeing’s fault. That’s an airline maintenance issue.
Unfortunately, the media don’t seem to be concerned with differentiating between Boeing problems and airline problems.
There is also concern that some planes already in service may have problems that will only appear in the future, some perhaps with catastrophic results. The Federal Aviation Administration is apparently investigating and may launch an inspection program to determine whether these concerns are valid.
The good news is these issues are not secret anymore and are being addressed. A quick look at a graph of Boeing’s stock price over the last 20 years shows just how costly these shortcuts have been from an investment perspective.
When we consider the loss of so many lives, there can be no justification.
The whistleblowers show that there are still employees who remember how it should be done. There are probably many employees who know this but are afraid to come forward. The risk must be eliminated, and they should be encouraged to share their knowledge. Once verified, the manufacturing and testing documentation must be updated to ensure these crucial steps become routine once again.
Boeing’s high-level managers and the newer employees have got to learn from these older employees who remember the crucial elements very quickly. Hopefully, Boeing can restore its reputation and the flying public can feel safe again.
Ronald J. Bourque, a consultant and speaker from Salem, has had engagements throughout the United States, Europe and Asia. He can be reached at 603-898-1871 or RonBourque3@gmail.com.